
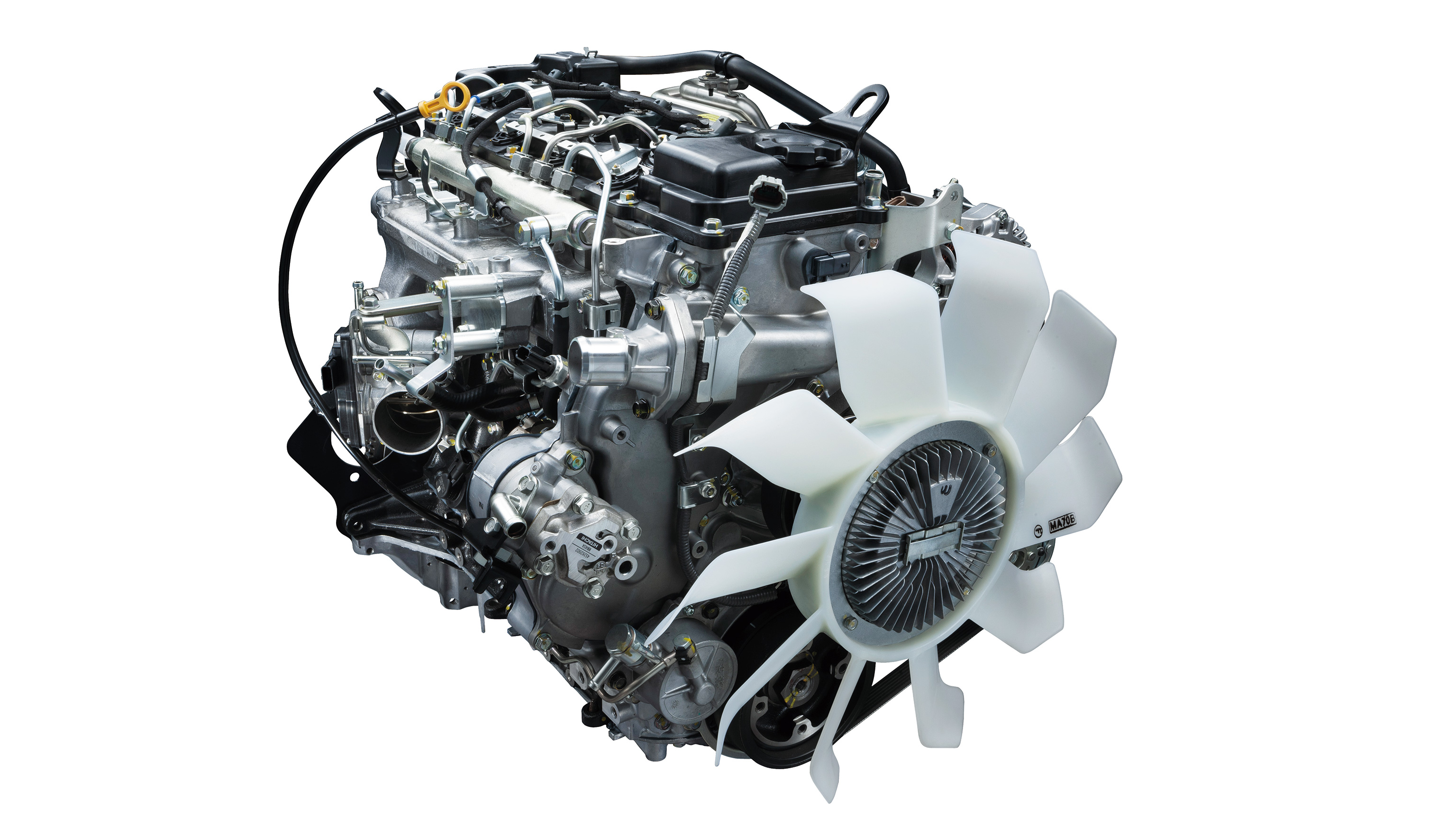
I think my next step is a careful costing exercise and some more market research into whether this is likely to be commercially viable. It is also a chance to optimise the design for reduced inertia. This would mean I could run an entirely Suzuki set up (cover plate, pressure plate and release bearing).
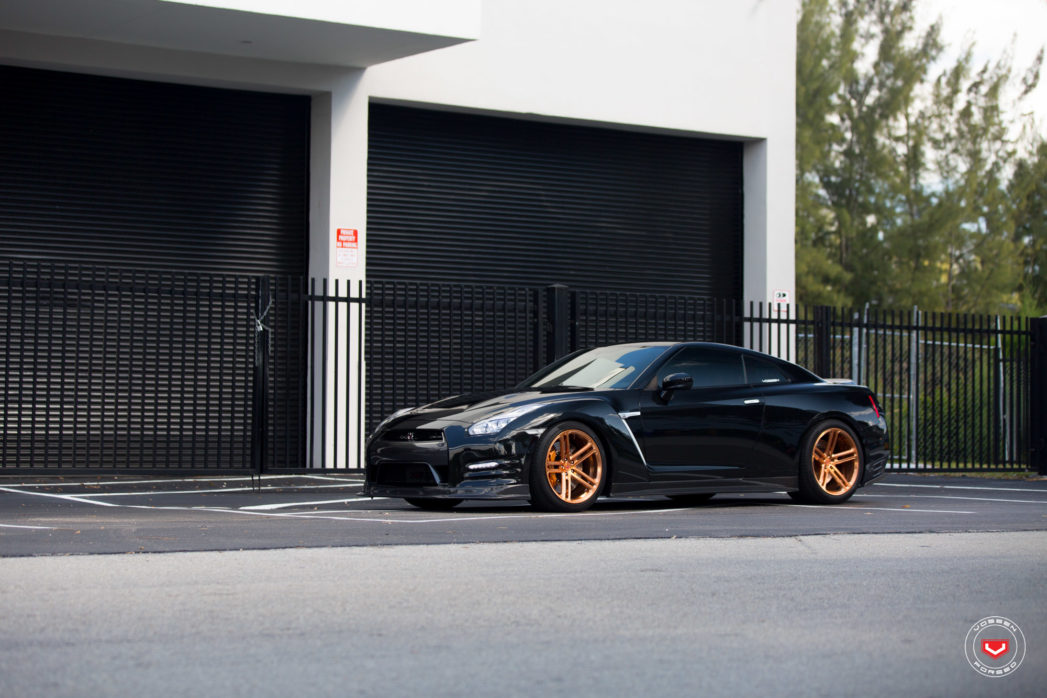
It also gives me freedom to incorporate the spigot bearing location into the flywheel and use any clutch combination I like.

This can be machined with a reduced diameter crank sensor cut outs, a thinner starter ring gear closer to the engine and the clutch spaced closer to the gearbox. What this ends up with is a functional setup with a lot of custom parts, a huge amount of rotating inertia and a hodgepodge of parts (modified Nissan flywheel, Mazda clutch plate, Nissan clutch cover, Suzuki release bearing, custom spacer, custom spigot bearing carrier etc etc). This could be resolved by spacing the entire clutch assembly out further towards the gearbox with a plate Having the clutch this close to the engine also means that it is not possible to use the Suzuki clutch release bearing as the guide tube is not long enough
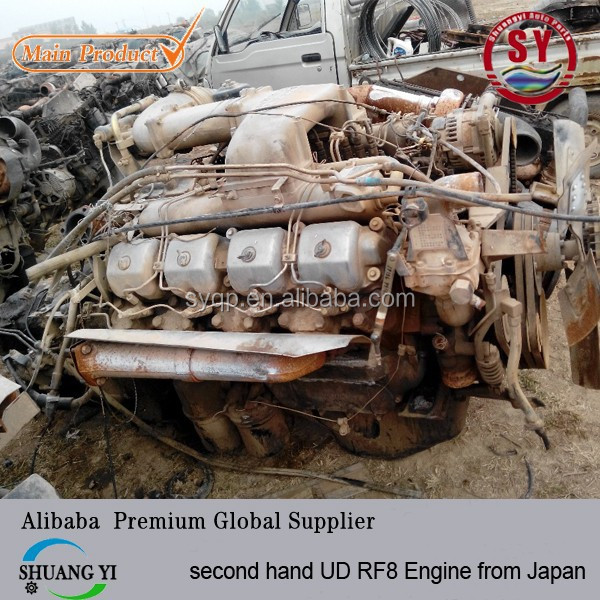
This would result in a problem with the clutch plate not being fully engaged on the input shaft splines.Ĭlutch plate (green) is not properly engaged on the splines. This would pull the flywheel further into the adaptor plate clearing the bell housing and would be a pretty simple modification to make. Mill 5mm from the crank mating face of the flywheel. However, it only protrudes by 3mm above the adaptor plate. This is too large to grind clearance for without compromising the strength of the box. The CPS teeth are size for size with the bell housing so I was able to get clearance quite easily with a carbide. The flywheel I am using has a standard ring gear and a smaller set of teeth for crank position sensing. What I failed to notice was the smaller bell housing casting! To counter this I decided to use the earlier G13BB gearbox which is almost identical externally but with a slightly different starter motor position and bell housing hole pattern. This puts the R7ME into higher demand in Jimny circles wanting to upgrade. However I found that the R7ME box was quite rare as it was quickly replaced with a R72 box, which is much more fragile. I was given a drawing of the bell housing profile by a very helpful member of the bigjimny forum which had ample clearance for the Micra (and A-Series) flywheel. Significantly less successful was the discovery that the flywheel doesn't fit in the bellhousing! When I first started researching the conversion I was looking at using a later R7ME Jimny gearbox from the twincam M13A engined cars. I will trim the housing a bit and probably move it forward 10mm to get a bit more clearance. Gear stick looks to be in the right place but is a bit tight. It is so light I can lower it in with one hand!
Nissan cg engine trial#
Not to be deterred I carried on with a trial fit in the car with the dummy blockįollowed by the block. I think moving forward I will abandon fully laser cutting the plate and either have a cut profile with milled holes or a fully milled part, depending on cost. The A-Series version was a complete ring so was more stable. I need to discuss the issue with the supplier when they are back next week as it appears that not all of the holes were cut before the outer profile was cut. However, holes that had lined up now didn't. Carefully manipulating it got the dowel holes in the block to line up, along with some of the bolt holes. I suspect this was due to stress in the steel so popped the plate in the press. Overlaying it onto a 1:1 print revealed that the entire form was distorted around the starter motor recess, splaying out. When I came to fit the new adaptor plate onto a block with dowels and all the fasteners it became apparent something was very wrong, several holes were 4 or 5mm out of position. Since last time it has started to feel like a bit of an uphill struggle. Samulis - I have been running the standard 1,3 cams but will be fitting some 774 rally cams when it all goes back together, the head is away being skimmed and ported which will bump the compression from 9,5:1 to 11,5:1.
